Sealing Vertical Turbine Pumps & Supporting Their Shafts
Vertical turbine pumps (VTPs) are used in numerous industries, including power generation, pulp and paper, mining, and water and wastewater. The shafts on these pumps extend many feet under the ground, sometimes as deep as 2,000 feet.
Because of this and the often harsh and remote conditions in which they operate, these pumps must be reliable. For them to be reliable, the bushings and seal technology installed in them must survive for long periods.
Proper VTP operation and mechanical seal life rely on several parameters:
selecting the correct mechanical seal
ensuring that these long shafts are supported and any movement is limited
keeping the seal cool and clean
IMAGE 1: A VTP with line shaft bushings in yellow and bowl bushings in blue (Images courtesy of SEPCO)
Selecting the proper bushings and mechanical seals help extend the pump’s life and prevent costly repairs.
This article will examine the operating and maintenance challenges of VTPs and how users can solve them with a combination of technology for prolonged pump life.
Maintenance Challenges
Operations often begin in dry-run conditions, which potentially overheat and damage traditional bushings and seals. There is a need for assets that can withstand this short-lived but harsh operation. In addition, dirt, rocks and other debris may be lifted with the water. This causes wear and damage to the shaft and/or the bushing if the bushing material is ineffective.
Another issue is shaft deflection or “the bending of a pump shaft that occurs when the velocity of liquid being pushed by an impeller is not equal at all points around the impeller.”1 This deflection causes premature packing or mechanical seal wear. It also results in flush water leakage and difficulty in controlling the flush water usage.
A Shaft-Support Solution: Self-Lubricating, Antiwear Bushings
Shaft deflection, damaged bushing and damaged seals are problems when using VTPs. The first step for reliable operations is stabilizing the shaft with bushings. Some bushings can stabilize shafts in:
overhung shaft designs
long shafts with little support (as in VTPs)
shafts with excessive runout causing premature mechanical seal and packing failure
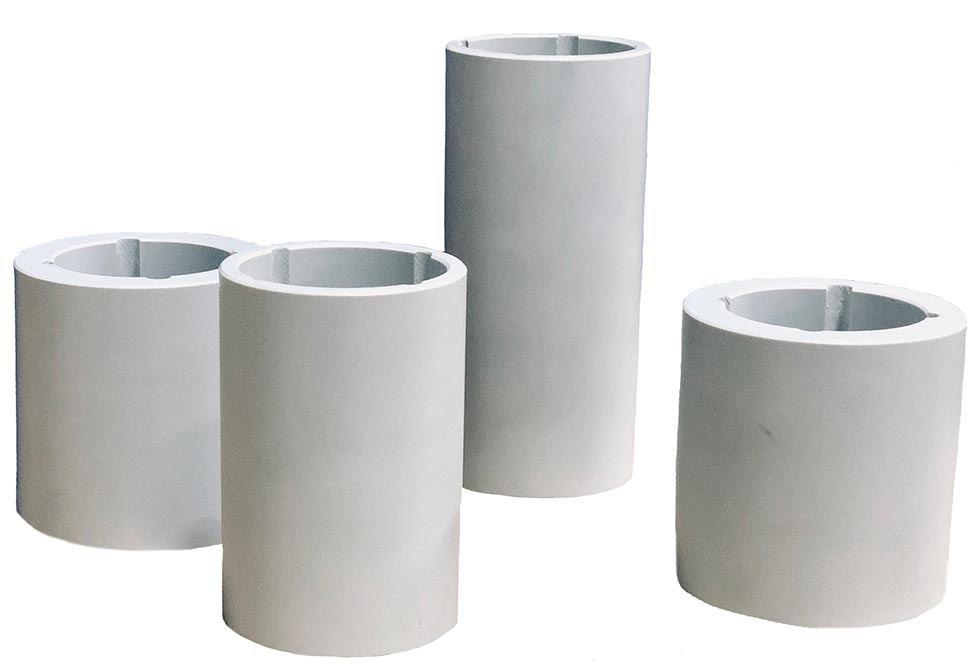
Bushings must be used along the entire length of a VTP shaft. In Image 1, the line shaft bushings are shown in yellow; the bowl bushings are in blue. Both types of bushings minimize shaft deflection.
IMAGE 3: Standard American Society for Testing and Materials (ASTM) test in dry-run conditions with no lubrication.
With reliable, self-lubricating bushings (Image 2) in place, wear is reduced even at startup and during dry-run conditions. End users should look for bushings proven effective and, ideally, have received independent testing and meet the parameters shown in Image 3.
Sealing Challenges
Sealing challenges travel hand in hand with maintenance challenges. Dirt, grit and rocks will move into the seal chamber/stuffing box with the liquid. To mitigate damage to the seal, proper flushing and cooling is required. In many VTP applications, clean water may be the best lubricant. However, end users and maintenance professionals should consult with the seal manufacturer.
Mechanical Seals Built for VTPs
When selecting a mechanical seal, the following operating parameters need to be considered:
pressure
temperature
shaft speed
pH of the pumped material
A cartridge seal with high radial clearances is ideal for VTPs. A cartridge seal that is completely self-contained, preassembled and preset before shipping simplifies installation. These features also support quick and easy impeller adjustments that do not interfere with the correct axial setting of the seal.
The seal’s life depends on choosing the most effective materials of construction and its operating environment. This environment includes how clean the seal chamber/stuffing box is, and how cool the faces are.
For a seal installed on a VTP, a vented gland eliminates air entrapment and improves cooling efficiency. Machined glands offer superior corrosion resistance and strength and can be modified to fit
the equipment.
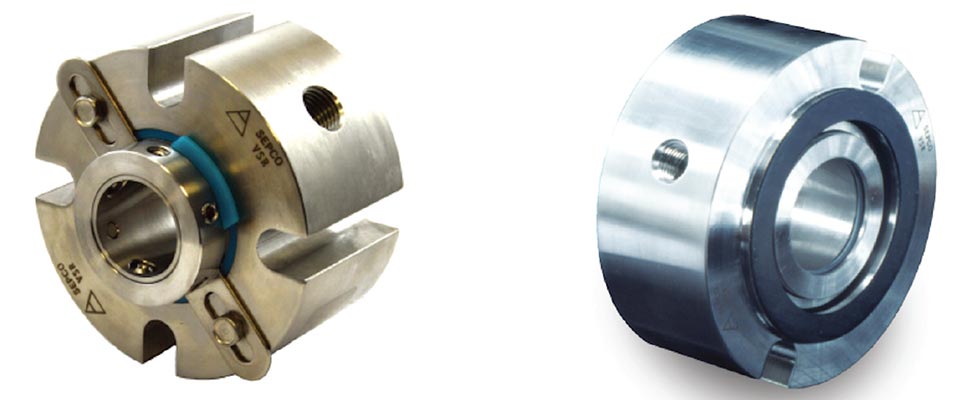