Containment Considerations for Magnetic-Driven Pumps & Designs for Integral Motors in Canned Motor Pumps
Q. What primary and secondary containment considerations are recommended for magnetic-driven pumps?
A. The principal design consideration for sealless pumps is to prevent leakage to the atmosphere. A magnetic drive pump (MDP) (see Figure 1) is a type of sealless pump that uses an outer ring of permanent magnets to drive an internal rotating assembly through a corrosion-resistant containment shell. The torque transmission by a magnetic coupling eliminates the need for a traditional shaft seal.
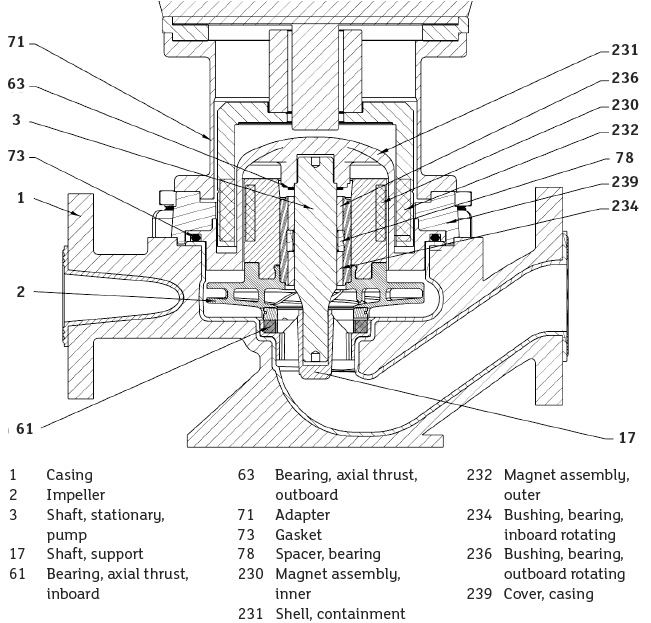
Because the primary containment could develop leakage as a result of wear by adjacent rotating parts, corrosion or abrasion, secondary leakage containment may be required. Secondary containment is a secondary pressure boundary that provides absolute containment of the pumped liquid in the event of a breached containment shell.
The construction material of the secondary pressure boundary must be evaluated to ensure it is compatible with the pumped liquid. The requirements and solutions for secondary containment vary based on the application and pump configuration, so the purchaser and pump supplier must discuss these points.
Primary and secondary containment will have design pressure ratings equal to or greater than the maximum working pressure of the pump at rated conditions. For MDPs, when primary or secondary pressure barriers are metallic, they are designed for the maximum allowable working pressure within stress values for the materials in Section VIII of the American Society of Mechanical Engineers (ASME) Boiler and Pressure Vessel Code.
Nonmetallic primary or secondary containment shells are substantiated through design and test to have a minimum ratio between bursting pressure and design pressure of 2-to-1 for the pressure/temperature range.
The secondary containment is designed to contain leakage for a minimum of 48 hours in the event of containment shell leakage and have a minimum standby life of three years. In the event of leakage through the containment shell, pump operation must be immediately discontinued. The pump user is responsible for providing shutdown devices and procedures required for safety.
For more information, refer to the newly revised standard ANSI/HI 5.1-5.6 Sealless Rotodynamic Pumps for Nomenclature, Definitions, Design, Application, Operation, and Test.
Q. What are the design recommendations for integral motors used in canned motor pumps?
A. A canned motor pump (CMP) (see Figure 2) is a type of sealless pump that combines a centrifugal pump and induction motor into one hermetically sealed unit. The motor rotor is typically supported by hydrodynamic bearings at each end, and the stator windings and rotor bars are protected from the process liquid by corrosion-resistant and nonmagnetic liners. The fluid—typically taken from the pump discharge or a flush introduced from an external source—is used to cool the motor and lubricate the bearings.
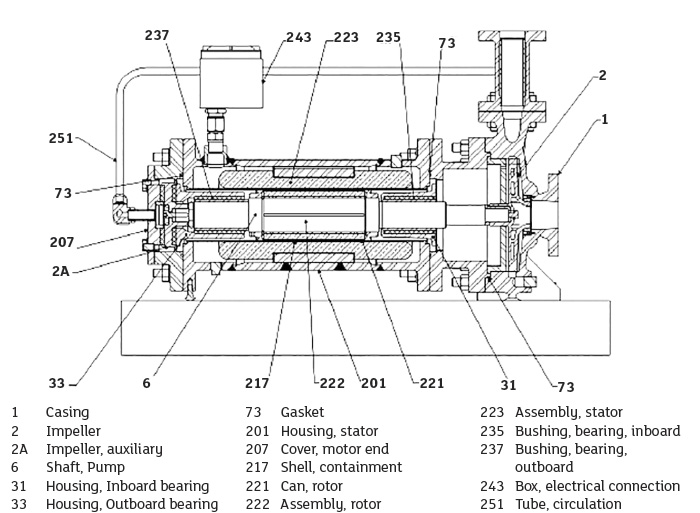
The circulation of pumped fluid in the motor must remove heat generated by eddy current losses, rotor windage loss and motor electrical losses. The stator winding temperature must be maintained at or below values established for the grade of wire insulation used in the stator windings. Thermal protection of the stator windings is provided along with the temperature setting. Additionally, the purchaser can specify a motor winding temperature rise test to verify that the motor windings will not exceed the maximum insulation temperature at design motor load and motor liquid cooling temperature.
For satisfactory life of the CMP, it is necessary to provide clean liquid (not vapor) for internal bearing lubrication and motor cooling over the intended pump operating range. This is done through unit design and selection of the proper circulation plan. Selection of a circulation piping plan depends on knowledge of liquid properties such as cleanliness, volatility, viscosity, specific gravity, toxicity, temperature, corrosiveness and any tendency to form solids.
Intended flow rates, net positive suction head available (NPSHA), frequency of starts, cooling or heating availability, and potential loss of suction liquid also should be considered. The purchaser must supply this application data for the manufacturer to recommend the most suitable circulation plan. Because internal flow is critical for reliable operation, instrumentation and controls to detect loss of flow through the drive unit are desirable.
When explosion-proof units are required, the manufacturer and purchaser must select the approved design that meets temperature, pressure and appropriate division, group and class requirements. Information on external motor temperature may be required by the manufacturer for proper selection.